【コラム】 製造業の社長に伝えたい![2] 第7回(最終回)
酒田 裕之( 生産管理コンシェルジュ )
2023年1月16日
製造業最大の経営課題は、社外的には納期短縮、社内的には固定費である工場の稼働率を上げることです。
その解決策の本命は、何と言っても工場の最適スケジュールの自動作成(自動スケジューラー)ではないでしょうか。しかし、私の知る限り、導入して成功している例は非常に僅かです。
なぜ成功しないのでしょう? 成功に立ちはだかる3大課題について、見ていきたいと思います。
【第1課題】 細かいマスターの準備が必要
自動スケジューラー導入のためには、生産管理よりもさらに細かいマスターが必要となります。
例えば、ある品目をある工程に設置されている機械で加工する場合のタクトタイム(1個あたりの加工時間)ですが、その加工が可能な機械が3機種あれば、機械ごとにデータを整備する必要があります。また、3機種の中でどの順番に割り振ればよいか、優先順位を決める必要があります。さらに、品目ごとに前段取り時間、後段取り時間を設定しないと、機械の時間割りつけができません。
まず、ここが第一関門ですが、これらのデータが揃っていないケースがほとんどです。機械作業日報そのものが存在しない、機械作業日報が存在しても時間データがおおまか過ぎて使えない、それでは、品目ごと、機械ごとに現場で作業時間を実測してサンプルデータを取ろうということになると、とても忙しくその時間が取れない、など、これらのデータを揃えるハードルは、相当に高いと言えます。
【第2課題】 100%を求める気持ちを抑えることが必要
第1課題をなんとか乗り越えると、次の課題が待っています。
実際の機械取り(機械ごとに製造品番の割りつけを行い、スケジュールを作成すること)では、前述の品目別機械別タクトタイム、前段取り時間、後段取り時間以外に、多くの判断要素があります。
例えば、同日作業となった品番が複数あった場合、どれを先に作業した方が段取り替えの時間が効率的かという判断が必要です。同じく、複数品番が同日作業の場合に、得意先の優先順位を配慮する時はどうするかも判断が必要です。
スケジューラーによっては、こうした判断を加味できる設定も可能ですが、加味するということは、さらに細かいデータを準備する必要があります。
例えば、前述の段取り時間の最適化をするためには、作業する前後品番の組み合わせごとに時間を登録することが必要となり、幾何級数的に整備しなければならないデータが増えます。そこで、前後工程の組み合わせによる効率化の判断はシステムで行わず、そこだけは人間が確認して、必要があれば修正するような落としどころを検討する必要があります。
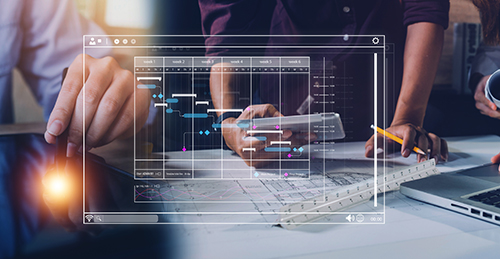
また、例えば第1工程が機械工程、第2工程が人中心の工程や外注工程、第3工程は再度機械工程の場合、第1工程でチョコ停(何らかのトラブルにより、数分から数十分程度、生産停止になること)が発生したり、第2工程で納期遅れなどが発生した場合、これらの情報が正確にシステムに反映されていないと第3工程の機械工程の計画の自動作成ができません。つまり、スケジュールの自動作成は、前工程の完了がリアルタイムにシステムに投入されていることが前提になるということです。もし、それが実現できないのであれば、第2工程以降の自動スケジュール作成はあきらめ、第1工程の機械工程だけ自動化させるなどの妥協が必要です。
上記のいずれの例でも、スケジュール作成を100%自動化することはあきらめ、確実に使える部分、つまり80%の自動化を狙う心構えが必要です。
【第3課題】 運用体制、ルールが重要
全自動でシステムがスケジュールを作成して運用可能となった場合は、「それに誰もケチをつけない」というルールを作ることが大切です。つまり、『システムの判断が一番偉い』という状態を維持することです。
スケジューラーが作成した結果の一部を見て、機械取りに経験のある人が「ここが違う」「あそこが違う」と言い始めることがあります。そこで、その人の判断でスケジュールに修正を入れてしまうと、システムが考えた全体最適の計画が崩れてしまうことになります。私は、それが理由でスケジューラー導入に失敗した事例を見たことがあります。
また、前述のように「同日作業の前後工程の組み合わせによる効率化の判断はシステムでは行わない」と決めた場合は、「ここだけは人間がチェックする」という運用が必ず必要になります。
つまり、システムで自動化する範囲を明確にして、システムと人の役割分担を明確にすることが非常に大切になってきます。
IoTの普及、AIの進展で、課題解決が容易に
以上、多く企業が困っている自動スケジューラー導入の課題について触れました。最後に、今後の展望について少し触れたいと思います。
まず、第1課題のマスターの整備の解決策として、IoTの普及により、機械作業時間や段取り時間の正確な取得が可能になってきている点が上げられます。これらのデータから、精度の高いマスターデータの生成が可能になってくることが考えられます。
また、取得した実績データをAIに学習させることにより、AIを活用した自動スケジューラーの可能性が出てきています。この場合、マスター整備の範囲が大幅に縮小され、精度の高い自動化の可能性も出てきます。今後のAIの動向に期待しながら、注目していきたいと思います。
これまで、「生産管理システム導入のポイント」について、業務に即して解説してきました。業務編は今回で最終回といたします。最後までお付き合いいだきありがとうございます。
次回は少し間をいただき、生産管理システムの導入前、導入後に、どのような取り組みが、生産管理システムのより効果的な活用につながるのか、事例を交えてながらお伝えしたいと思います。
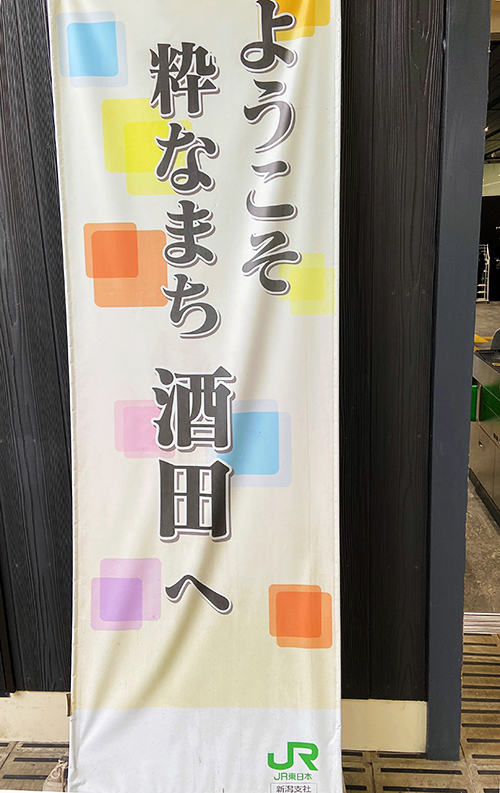