【コラム】 製造業の社長に伝えたい![2] 第2回
酒田 裕之( 生産管理コンシェルジュ )
2022年8月17日
在庫削減目標に到達しない原因は?
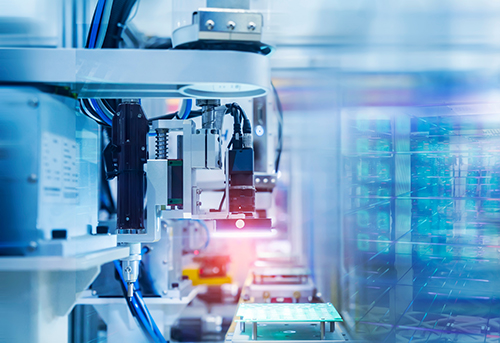
在庫がリアルタイムで見えるようになり、不足する手前で手配できるようなり、在庫数が多いようであれば手配を少なくすることができるようになったはずです。しかし、想定していた在庫削減目標に達していない、というケースがあります。なぜでしょうか?
いくつか原因を考えてみましょう。
(1)マスターの設定を定期的に見直しているか
考えられる1つ目の原因はマスターの設定です。過去のコラムでも何度か触れていますが、このことが原因であることが非常に多いのです。
具体的に言うと、生産管理システムに設定されている在庫マスターの最低在庫数が導入当初の設定のままになっていて、定期的に見直していないということです。
導入当初は欠品しないようにと安全を考えて、最低在庫数を多めに設定することが多いのです。しかし、その設定値を実情に合わせて見直していないと、最低在庫数が必ず在庫となってしまうため、在庫が多くなってしまうことがあります。
(2)発注リードタイムを長めに設定していないか
考えられる2つ目の原因は、購買マスターの発注リードタイムが長めに設定されていることです。
リードタイムが長めに設定されていると、なぜ在庫が増えてしまうのでしょうか。「必要数を早めに手配できるので、良いことでは」と思う方もいらっしゃると思います。しかし、手配後に需要(必要数)が減った場合を考えてみてください。そのままにしておくと、余分な在庫が多くなってしまいます。リードタイムをもっと短く設定しておけば、需要が減った時の最新の情報をもとに手配できるため、手配数を少なくでき、在庫を増やさずにすみます。
(3)適切な手配方法を選んでいるか
個別に手配する方法(製番手配)とまとめて手配する方法(MRP手配)の違いによって、在庫が増えてしまうケースがあります。
製番手配とは、受注や製品ごとに部品を発注する方式です。MRP手配は、指定の受注や製品ごとではなく、同じ部品であれば共通に手配する方式です。
この違いを具体例で見てみましょう。
Aという製品を100個つくるにはaという部品が100個必要だとします。一方、Bという製品を100個作る場合には、aという部品が200個必要だとします。そして、aという部品は最低300個からしか手配できない(最低発注ロット)部品だとします。
別々に手配する製番方式だと、A用に300個、B用にも300個手配せざるをえず、結果、300個が余分の在庫となります。一方、共通手配するMRP方式の場合は、AとB両方で使う300個をそのまま手配できるため、手配した部品はすべて使い切り、在庫はゼロになります。
このように、マスター設定や手配方法が原因で在庫が適正にコントロールされていないと、生産管理システムを入れても在庫が減らないことがありますので注意が必要です。
在庫削減には、的確な需要予測(販売予測)が重要
需要予測(販売予測)に合わせて生産計画を立てている場合、需要予測(販売予測)が的確でないと、製品在庫が増えてしまうことがあります。
製品の需要予測(販売予測)を立てるのは難しいものです。どうすれば的確な需要予測(販売予測)ができるかを見ていきましょう。
営業部門の理解と協力が必要、AIの活用も
例えば、製品の製造納期(材料、部品納期+加工・組立納期)が6ケ月かかるのであれば、6ケ月先までの販売予測を立てる必要があります。さらに、この作業は全対象製品に対して毎月、見直していく必要があります。
この作業は営業部門に多大な工数をかけることになりますので、なぜ販売予測が必要なのか、十分な理解を得られるように営業部門とのコンセンサスが必要となります。最近では、過去の販売実績データをAIで学習させ、販売予測を立ててくれるソフトなども出ていますので、うまく活用していきたいところです。
会社は未確定情報の重要性を認識すべき
自動車部品の製造業では、受注の大元である自動車メーカーが、毎月内示受注情報を3ケ月先まで提示してくれ、1ケ月前になると確定受注情報を提供してくれます。
本来であれば、確定受注がきてから生産計画を立て、材料手配をしたいところですが、それでは間に合わないものは内示受注情報の段階で手配します。その後、正式に来た確定受注情報が内示受注情報より少ない場合は、材料在庫が多くなってしまうので、発注を少なく修正します。修正できない場合は、次の出荷用在庫に充当するなど、在庫が増えないようにする必要があります。
このように、注文がきてから作ったり、材料手配していたのでは間に合わない場合は、販売予測や内示受注情報などが在庫削減に非常に重要になります。会社はこうした未確定情報の重要性を認識する必要があります。
営業部門とのコンセンサスが「在庫削減の肝」
これらの未確定情報の精度を上げていく上で重要なのが、得意先からの受注の窓口となっている営業部門と生産数を決める生産管理部門のコンセンサスです。営業部門と生産管理部門が利害(営業は欠品したくないので多く作りたい、生産管理部門は効率よく適正在庫を維持したい)を超えてコンセンサスがとれるかどうかが「在庫削減の肝」となるのです。
生産管理システムは稼働しているのに在庫が減らないとお悩みの方は、以上のことをチェックしてみてください。
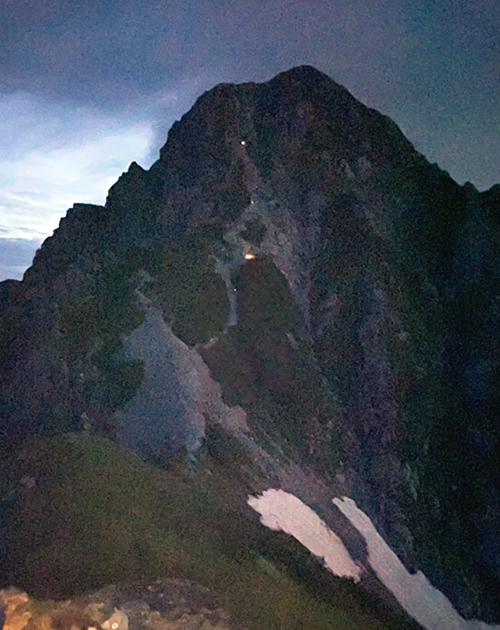