【コラム】 製造業の社長に伝えたい![2] 第1回
酒田 裕之( 生産管理コンシェルジュ )
2022年7月19日
これまで9回にわたって、生産管理システムの導入プロセスで準備すべきこと、知っておいて準備をすれば導入がスムーズにいくポイントなどについて述べてきました。今回からは、「生産管理システム導入のポイント(業務編)」として、実際にシステムを入れてみて感じる業務の落とし穴とその解決方法について、経験談を交えてお話していきたいと思います。
ぴったり合うはずの在庫数が合わない
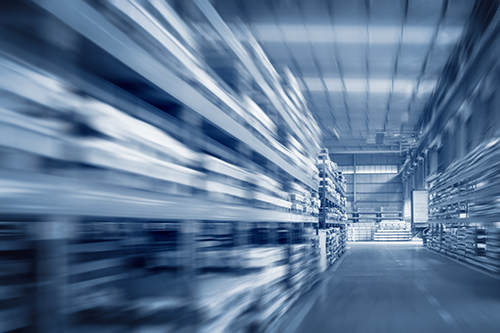
コンピューターの在庫数は、入庫でプラス、出庫でマイナスをする仕組みです。よって、一旦在庫を数えて、その数を登録したあとは、正しい入庫入力と出庫入力が行われれば、システムの在庫数と実在庫はピッタリ合うはずです。しかし、実際はなかなか合ってきません。何が起きているのでしょうか。
(1)入庫数の入力にタイムラグが生じる
まずは入庫からみていきましょう。
例えば、材料を仕入れて、倉庫に入庫した後、納品書や送り状をもとに、入庫入力を行うのですが、これがすぐに行われないケースがあります。
[ケース1]発注書の番号を調べるのに時間がかかる
入庫入力と同時に、発注データの消込も行うため、発注書の番号が仕入先からの納品書や送り状に記載されていない場合などは、その番号を調べるまで入力できません。その間に半日から一日経ってしまうと、入庫数にタイムラグが生じます。
[ケース2]入荷場所と入力場所が違う
入荷場所が倉庫で、入庫入力する人が事務所にいる場合などは、納品書や送り状が倉庫から事務所に移動するまで入力ができません。そのため、タイムラグが発生します。
これらの場合、コンピュータ上の在庫が、一定期間少なくなります。
(2)納品書の数と実際の入庫数が違う
納品書や送り状の数と実際に入庫してきた数が違っている場合があります。入庫数を数えている場合は、その場で入庫数を訂正することができますが、いちいち数えられない場合は、伝票の数が正となり、システムにはその数が入力されます。
入庫時に検品している場合は、そこで不良品が見つかったら返品処理します。検品していない場合は伝票の数が在庫となり、不良が見つかった段階(後工程の製造工程など)で、マイナスすることになります。
(3)出庫の際にミスが発生する
次に出庫について見てみましょう。
部品の出庫の場合、製品の製造に必要な数をシステムが算出して、倉庫へ出庫指示が出されます。その数を数えて出庫しますが、数え間違いが発生することがあります。また、似たような部品が多くある場合は、間違って別の部品を出庫してしまうケースも発生します。
(4)伝票を起こさず、部品を倉庫から持ち出すことも
実際に製造現場で製造していると、製造不良が発生して部品が不足することがあります。その際は、追加で部品の出庫依頼をした上で、部品を出庫する必要があります。しかし、製造現場の方が倉庫に入れる場合などは、急いでいるために伝票を起こさず、不足している部品を無断でもっていってしまうことがあります。
(5)現場で使った数、余った部品の報告、現場から倉庫への戻しがきちんとされない
あらかじめ不良を見越して、必要数よりも多く現場に出庫指示するケースがあります。この場合は、実際に使った数を報告し、余った部品は倉庫に戻す必要あります。
さらに、当該の製造向けに部品を個別に仕入れているケースでは、例えば必要数が1個でも、最低で買える数が10個の場合は、製造現場に直接10個届くことがあります。この場合は10個のうち1個を製造現場で使用し、残った9個は倉庫に戻す必要があります。
解決法は、運用ルールの取り決めと遵守です
このように、実際に発生する入庫・出庫の作業と、システムへの入庫・出庫入力の作業のズレから、「実在庫数とシステム上の在庫数が合わない」ということが起こります。
解決策としては、この二つがなるべく時間差なく、正確に行われるように、運用ルールを整理する必要があります。皆が使いやすい運用ルールを取り決め、それを遵守する体制を地道に作っていくことが必要となります。
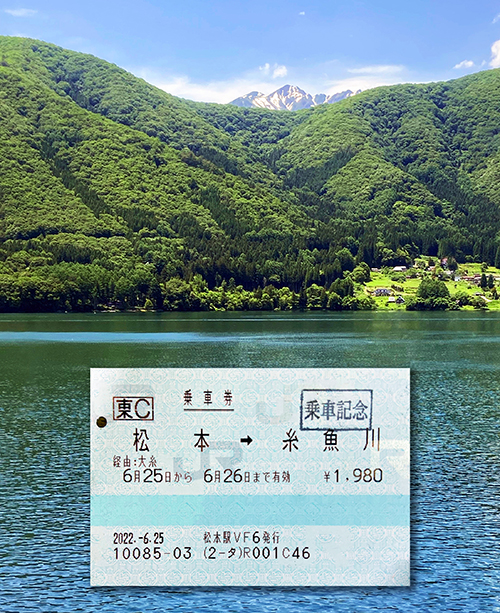